Adapting to Current and Emerging Trends in Manufacturing
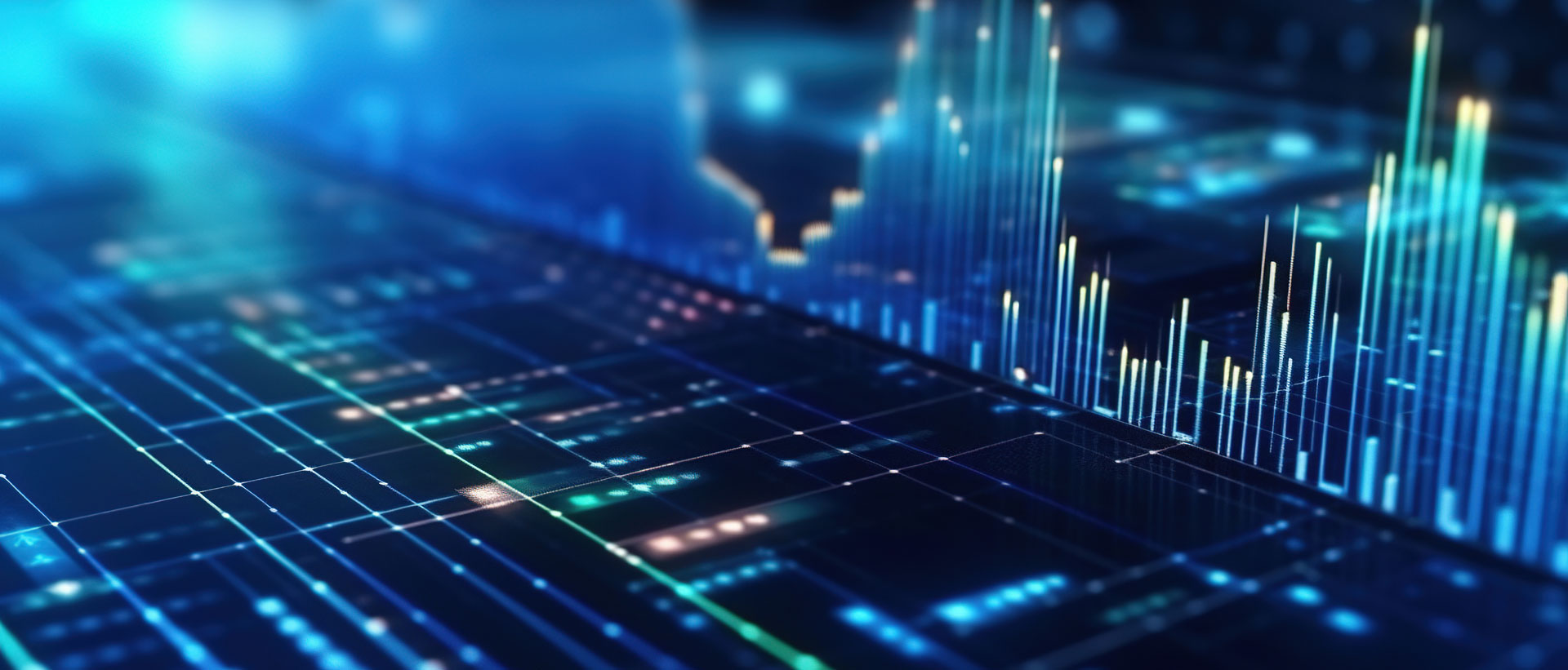
Looking back over the last five years, there have been many shifts in the manufacturing industry – precipitated by everything from rapid technological advancements and evolving consumer preferences to a global pandemic. With all that in mind, it’s safe to say the manufacturing industry is a landscape of continual change. So, what’s to come?
Take a look at the strategies and innovations driving adaptation in the manufacturing sector as we explore how manufacturers are staying ahead amidst dynamic shifts. From embracing automation and digitalization to meeting the demands for sustainability and supply chain resilience, continue reading to learn how to navigate current and emerging trends.
Implementing Generative AI and Data Utilization
The rise of generative AI (genAI) is prompting manufacturers to reassess their data utilization across the board with a vast amount of potential applications. Machine learning algorithms, for instance, can accelerate innovation by swiftly analyzing extensive datasets, including market trends and customer preferences, to uncover patterns and generate novel ideas.
GenAI also enables predictive maintenance in factories, leveraging real-time sensor data to identify anomalies and prevent equipment breakdowns, leading to substantial cost savings and operational enhancements. It’s important to recognize how genAI can enhance decision-making processes by rapidly analyzing historical data and generating actionable insights to optimize strategy and operations.
Transitioning to Smart Factories
More manufacturers are embracing smart factories by integrating advanced technologies like AI, 5G, IoT, data analytics and cloud computing. These technologies offer many benefits, from enhancing asset efficiency and productivity to reducing costs and improving safety and sustainability.
Despite initial hurdles like staff training and equipment upgrades, investing in digital strategies promises long-term advantages such as cost savings, heightened efficiency, productivity and a competitive edge.
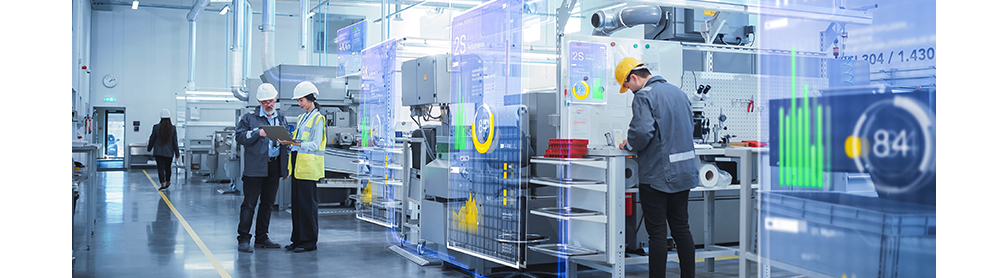
Reshoring and Maintaining a Steady Supply Chain
Since the onset of the COVID-19 pandemic, manufacturing firms have grappled with persistent disruptions in their supply chains, impacting production schedules, lead times, delivery and spending. These challenges stem partly from the aged practice of outsourcing parts and electronics manufacturing to reduce costs, leaving companies vulnerable to geopolitical tensions and energy shortages.
Consequently, there’s been a growing trend toward establishing domestic supply chains to bolster resilience and reduce reliance on foreign sources. Legislative efforts like the CHIPS Act, IJIA and IRA aim to incentivize reshoring.
Embracing reshoring and digital technologies represents a crucial strategy for manufacturing companies to fortify their supply chains against future disruptions and macroeconomic uncertainties.
Addressing Labor Shortages
Labor scarcity has been a persistent issue in manufacturing. According to the National Association of Manufacturers, nearly three-quarters of manufacturing executives identify attracting and retaining a skilled workforce as their primary challenge, with quit rates reaching 40% in 2023.
To address this, manufacturers are turning to technology and AI to engage and retain workers, reshaping training programs to prioritize data analytics and AI skills. Technology and automation can also complement human labor, reducing the need for additional hires and saving your company money.
Working Toward Carbon Neutrality
Manufacturers are increasingly focusing on sustainability and carbon neutrality as a response to growing investor and consumer interest in Environmental, Social and Corporate Governance (ESG) and net-zero carbon emissions.
In 2023, federal funding and incentives, like those from IIJA and IRA, supported electrification and decarbonization efforts, including investments in EV charging infrastructure and battery manufacturing.
To address these demands, manufacturers are adopting strategies such as partnering with sustainability-focused collaborators, investing in electrification and low-carbon technologies and establishing specialized divisions for zero-emission products.
Another way to stay on top of the trends is by keeping up with the latest rules and regulations.

View our checklist outlining the latest updates you should know from OSHA.