Raising the Bar: My Role in Standardizing Warehouse Excellence
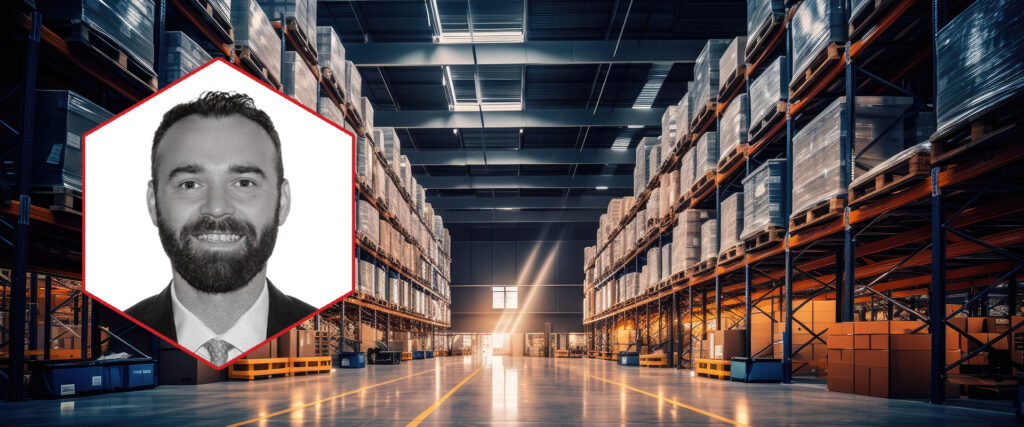
Contributed by Herb Kent, Customer Care Manager, 2 years
During my time leading the Boston warehouse, I had the opportunity to take part in something pretty special: RSH Warehouse Optimization and Standardization project. Though I’ve since moved on from that role, the changes we made together are still shaping how that warehouse—and many others—runs today.
When I got involved in the project, I didn’t quite realize how impactful it would be—not just for our Boston division but the way we strategically think about warehouse operations. That started as a 12-week initiative and ended up reshaping how we work, collaborate and prioritize safety.
Joining the Movement
I joined the project during phase two. The first phase covered six divisions and then eight more were added during phase two—including Boston and North Carolina. We were chosen from the East Region to implement the new standards. The program was led by Regional Operations Managers Joe Russo and Thomas Stockton and Supply Chain Director Jim Gerhart. They put together a detailed roadmap for us to follow.
The goal was bigger than just making all our warehouses look the same. Each warehouse is different—different layouts, different customer needs—but we wanted to establish a standard for things like signage, cleaning products, hazmat handling and, most importantly, training. The idea was to create a more unified, safer and more efficient way of operating.
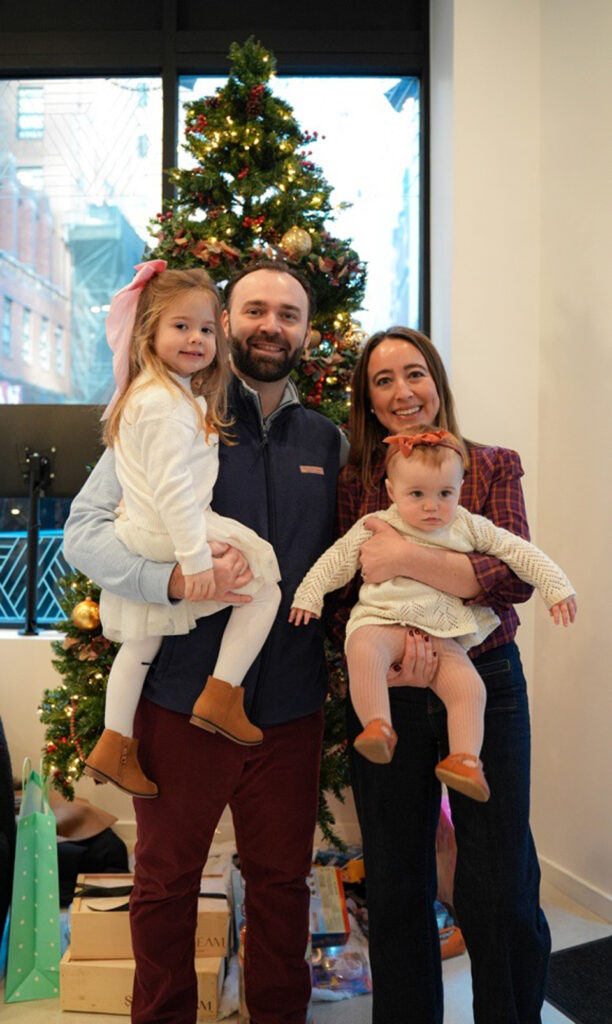
The “U” Model: Small Changes, Big Impact
One of the key ideas was adopting the U-shaped distribution model: product comes in one door, moves across the workspace and goes out another. It might sound simple, but that flow had a significant impact on our day-to-day warehouse operation. We invested in new tables, better signage, improved safety gear and updated cleaning supplies.
For our team in Boston, the biggest win was optimizing our inbound receiving process. We used to work in a cramped, undefined area. Now, we’ve got a dedicated 15-foot table that’s easier on the body and the mind. Returns, damages and defects are processed more efficiently, and everything just feels more organized.
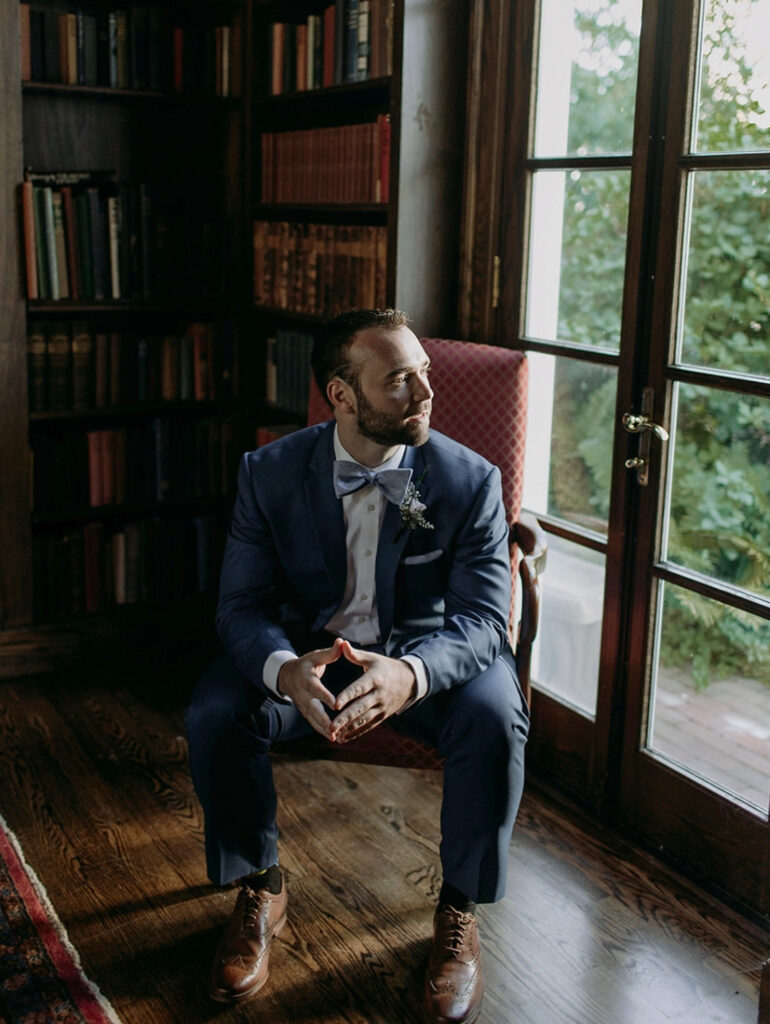
Safety First, Always
I’m a big proponent of safety, so having clear signage for forklifts, hazardous materials and fire extinguishers—it matters. It shows that the company is investing in its people. And that’s powerful.
We all went through standardized training programs, and at the end of the program, we completed additional HAZMAT certification requirements. We updated HAZMAT protocols, got our DOT paperwork in order and did full competency evaluations. It wasn’t just about passing a checklist—it was about raising the bar.
Collaboration Across Divisions
One of the unexpected highlights for me was the collaboration. Throughout this project, I worked with individuals from the Central and West Regions. It created a real network. We were solving the same problems together, learning from each other and sharing best practices. That connection made the process even more rewarding.
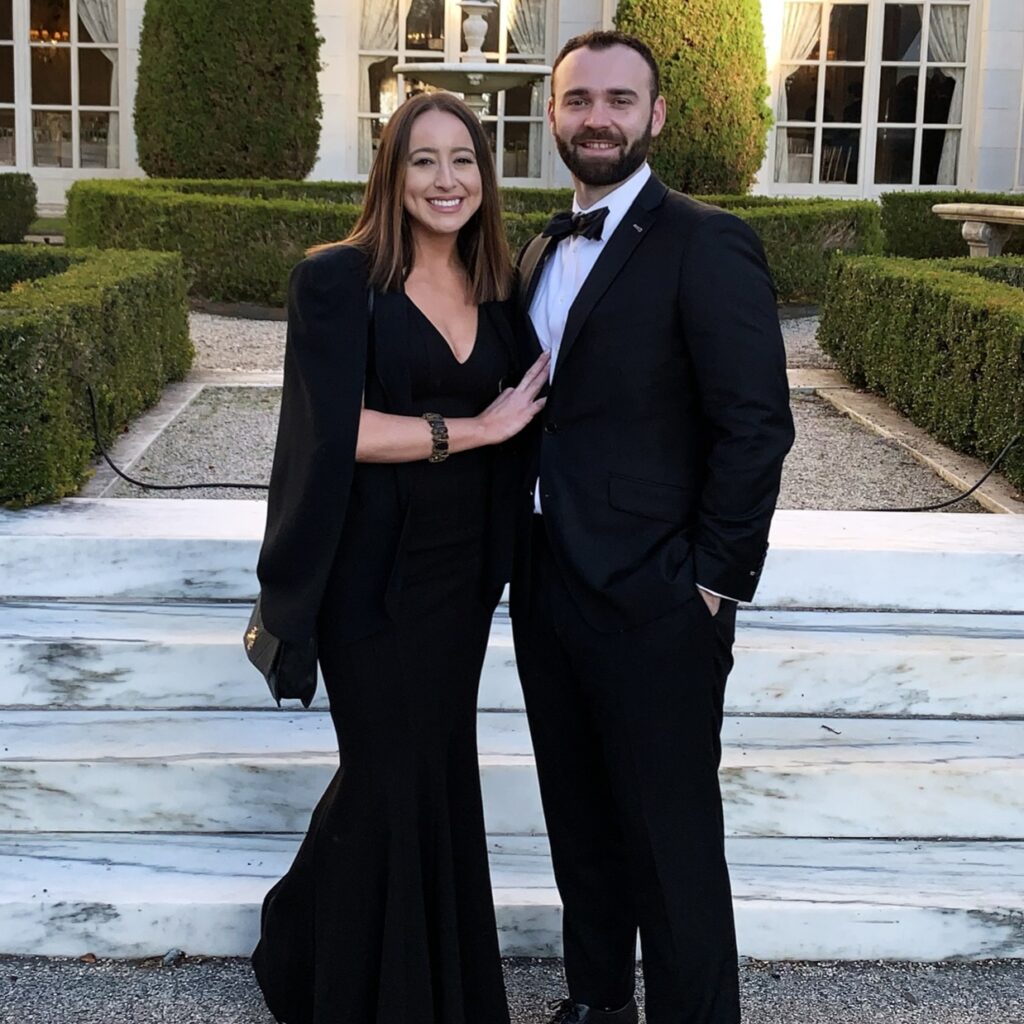
A Better Experience for Everyone
Even though I’ve stepped away from that role, I’m confident the changes we made didn’t just help our team—they helped our carrier partners, as well. UPS, FedEx, LTL drivers—they all know exactly where to go now. Doors and bays are clearly labeled, hazardous areas are marked off and we’ve eliminated a lot of confusion and risk. Even our SupplySight team has more space to stage their orders. Everyone benefits.
We also had to tackle some technical infrastructure challenges. Our networking room had been patched together over the years, and the wiring was a mess. We cleaned that up, made it safer and made sure we were set up for long-term success.
The Results Speak for Themselves
While I don’t have the exact data in front of me, I’m confident there has been a big improvement in our cycle counts, mis-shipments and inventory accuracy. We’ve made huge gains in our inbound and outbound efficiency. And just as importantly, the team felt it. They felt safer. They felt more valued. And that matters just as much as any data point.
This experience has shown me what’s possible when we put people, process and safety at the center of what we do. We’ve built something that’s not just better—it’s built to last.