How the New Brady i7500 Solves 5 Common Label Printing Problems
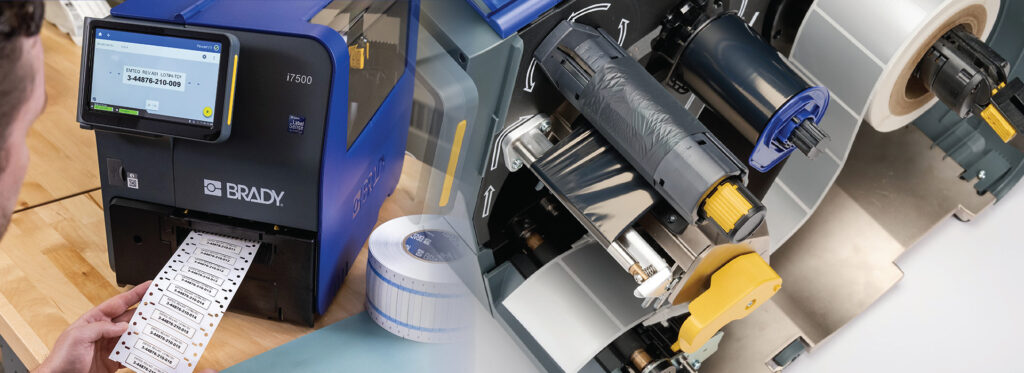
High-demand label-making environments require high-level efficiency, accuracy and reliability. Yet, many professionals face frustrating challenges with their label printers—frequent jams, slow changeovers, inconsistent print quality and complicated setups, slowing operations. Luckily, there is a solution.
Brady’s i7500 is transforming label printing with its smart design and consistent production. This new model is designed to reduce waste, improve efficiency and simplify operations. With its zero-waste printing, smart automation and user-friendly features, the i7500 is a true game-changer in the industry.
In this article, we will explore these five common problems and how Brady’s i7500 solves them, optimizing your label-making operations.
1. Jams and Wasted Materials
Conventional printers often require manual adjustments during operation. If this isn’t done correctly, it can lead to jams, misfeeds, inconsistent printing and wasted materials, resulting in wasted time and money.
The i7500 doesn’t require manual adjustments for print speed, heat settings, offsets or sensor modes, helping to eliminate trial-and-error printing. With its enhanced intelligent automation and precise adjustments, the i7500 can achieve perfect labels on the first attempt, lowering material costs and minimizing environmental impact.
2. Slow Changeover
Slow, complicated changeover is a common bottleneck for label printing. Printers commonly require users to manually adjust settings, align labels and fine-tune ribbon tension whenever switching materials or label sizes. This approach wastes time and increases the risk of printing errors.
The i7500 elevates efficiency standards, offering swift material changeovers. With its quick ribbon removal and user-friendly loading mechanisms, transitioning between jobs becomes a seamless experience in just 40 seconds without wasted materials or misprints.
3. Complicated Interfaces
Printers commonly require complicated configurations and time-consuming manual setups. They use non-intuitive controls, forcing users to navigate complicated menus. These complicated controls slow down printing jobs, leading to bottlenecks, training inefficiency and wasted time.
Brady integrates LabelSense™ technology into the i7500 to improve efficiency and user-friendliness. Featuring a 7-inch touchscreen, the printer’s interface enhances the printing experience by making it approachable for everyone. It minimizes the need for technical knowledge by providing on-screen guided prompts, simplifying setup and training.
4. Slow Printing Speeds
Keeping up with high-demand jobs is a common challenge for conventional printers. They are often slow, frequently pause, overheat, jam and regularly need to be recalibrated, slowing down production.
Designed for high-demand environments, the i7500 can handle over 7,000 labels per day. It prints faster without sacrificing print quality and its reliable performance minimizes maintenance-related downtime, improving speed and efficiency for each job.
5. Inconsistent Quality
Producing crisp, high-contrast barcodes and text without smudging, fading or illegible labels is another common challenge. This is caused by low-resolution print technology, inadequate material compatibility and subpar ink or ribbon performance. Without precise print calibration and high-quality label materials, printers will fail to create consistent quality.
With its intelligent automation and precise adjustments, the i7500 achieves perfect labels every print. Its high-precision printing technology ensures crisp barcodes, text and graphics. Brady also offers durable label materials designed to resist heat, chemicals and abrasion, improving efficiency and quality on every job.
Improve your label printing process today!