Case Study | How M.H. EBY Saved Over $85k With R.S. Hughes’ SupplySight Program
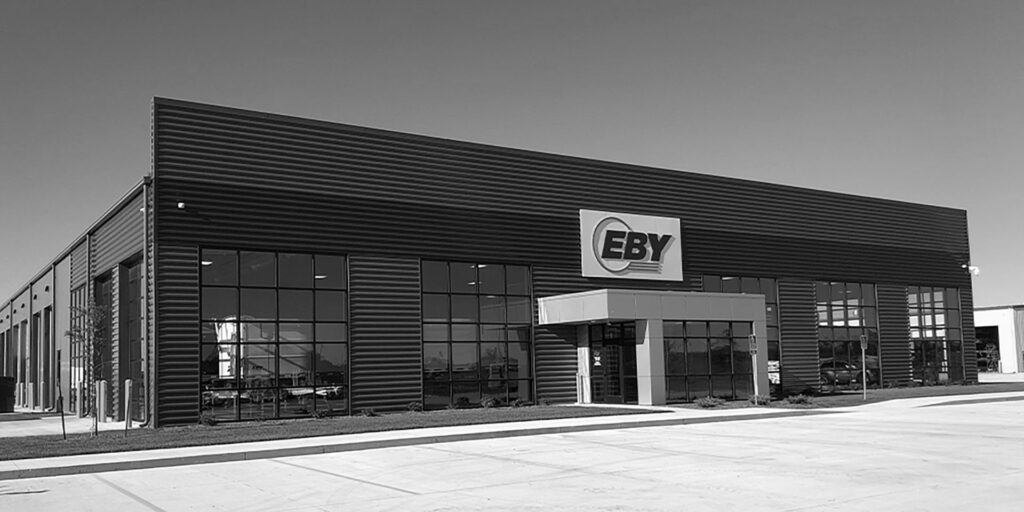
Overview
M.H. EBY is a prominent manufacturer of aluminum trailers and truck bodies with three key production facilities in Ephrata, Pennsylvania, Story City, Iowa and West Jefferson, Ohio. The company initially approached R.S. Hughes through a connection with Loctite, seeking solutions to improve pricing and local stock availability across their facilities.
R.S. Hughes enabled M.H. EBY to enhance its supply chain efficiency and achieve significant cost savings through strategic initiatives and tailored solutions—setting a solid foundation for continued success and growth throughout our partnership.
Customer Background
M.H. EBY started working with R.S. Hughes in December 2018, initially focusing on securing contract pricing and stocking items locally for their manufacturing needs. The collaboration expanded over the next several years, leading to a national account agreement with Nick Longenbach, one of our National Accounts Senior Representatives.
Through collaboration with Andy Derr, M.H. EBY Operations Manager, and Doug Beaver, M.H. EBY Purchasing Manager, Nick gained an understanding of their top challenges and got to work building custom solutions.
Challenges
M.H. EBY faced several challenges:
- Disparate Purchasing Practices
Each of M.H. EBY’s three manufacturing sites purchased inventory independently, leading to inefficiencies and missed opportunities for cost savings. - Lack of Data and Visibility
The company needed more insight into its purchasing habits, spending patterns and inventory management. - Need for Standardization
A standardized list of approved items was needed to ensure consistency and control across all locations.
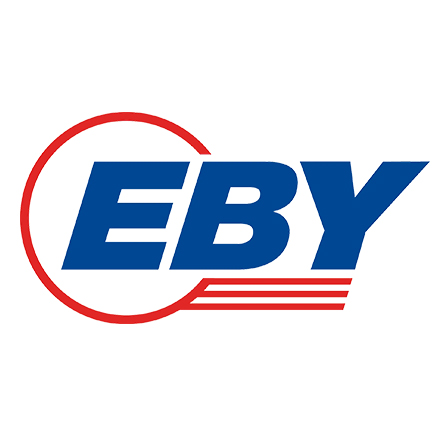
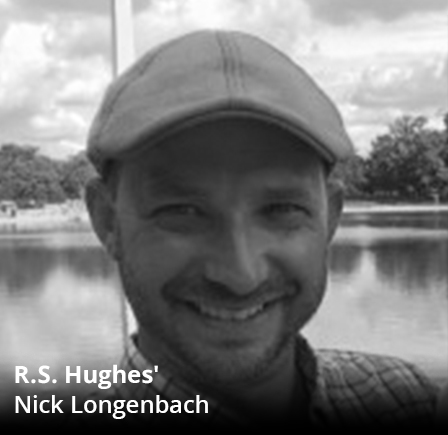
R.S. Hughes’ Solutions
To address M.H. EBY’s challenges, R.S. Hughes implemented a series of strategic initiatives:
- National Agreement and Uniform Pricing
We negotiated a national agreement to provide uniform pricing and discounts across M.H. EBY’s three locations in Ephrata, PA, Story City, IA and West Jefferson, OH. This move was designed to leverage their collective buying power, resulting in significant cost savings. - Integrated Inventory Management (IM) Program
Beginning with the Ephrata site in March 2019, we developed an IM program that provided a standard list of approved items for all locations. This program was subsequently rolled out to the Story City and West Jefferson sites. - Implementation of Vending Machines
In December 2023, we began deploying vending machines at the Ephrata site. We are also rolling them out to Story City and West Jefferson. These machines facilitate easier access to essential supplies and further streamline inventory management.
Customer Results and Benefits
The implementation of these solutions yielded significant benefits for M.H. EBY:
- Cost Savings
M.H. EBY’s national agreement with R.S. Hughes and streamlined operations have resulted in over $85k in cost savings across their three facilities. - Operational Efficiency
The introduction of vending machines improved accessibility to essential items, reducing downtime and enhancing overall productivity. - Enhanced Data Visibility
The IM program provided detailed insights into their purchasing habits, allowing corporate management to have control over approved items and standardize procurement processes.
“Setting up vending machines for PPE and shop supplies is saving us money. They’re super easy to implement, and it’s easy to track the costs and quantities of items being vended. Less downtime, less waste—it’s a win for our efficiency and cost savings.”
—Andy Derr, M.H. EBY Operations Manager
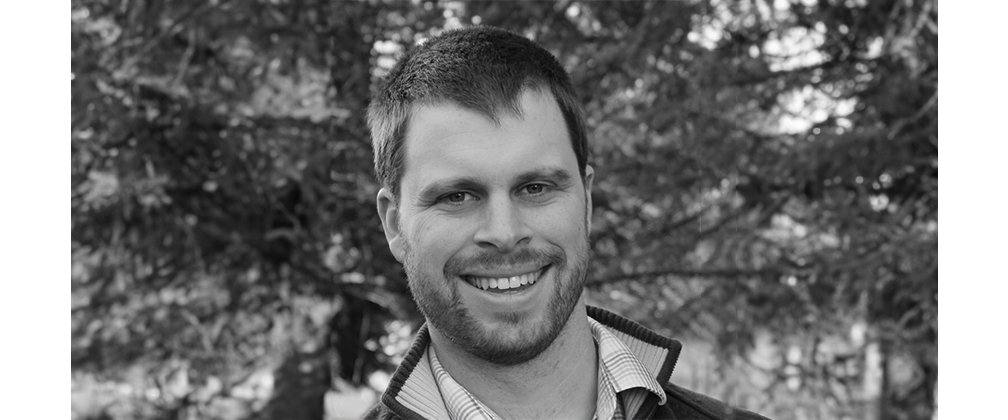
Future Prospects
Given the success of these initiatives, M.H. EBY is positioned for continued growth and efficiency improvements. Our robust relationship and collaborative efforts in implementing SupplySight™ will continue to streamline their supply chain, helping M.H. EBY grow into the future.
Learn About SupplySight™ Solutions for Your Business.